CLT, glulam deliver strength, low profile, and aesthetics for B.C. office building
When he set out to design his company’s new headquarters building on Lakeshore Road in scenic Kelowna, B.C., Tim McLennan of Faction Projects knew quickly that cross-laminated timber (CLT) was an ideal material. Several of CLT’s key attributes, including a slim profile, fire resistance ratings, ease of installation, and beauty, all contributed to the project’s success.
Developed, designed, and built by Faction’s integrated team, the 14,000-sf office building will also house leased tenants.
It was the project site, which backs up to Mission Creek and a greenway system in an area that's home to resort developments and residences, that drove McLennan’s overall design direction. “We wanted to build in a way that didn’t overwhelm the low-density neighborhood,” he says. “We looked for opportunities to screen views and protect them.”
To achieve the smaller scale without sacrificing profitable density, McLennan looked to the overall building layout and the structural materials themselves.
The building is framed with glulam post and beam, with CLT making up the floor and roof systems. Cross-laminated timber is a three-, five-, or seven-layer wood panel, with each layer oriented crosswise for increased dimensional stability and strength. As a result, CLT provides an unprecedented level of structural integrity, design flexibility, and cost-competitiveness.
For the Kelowna project, the team used seven-ply CLT from Structurlam Products Ltd. for the floor systems and five-ply CLT for the roof. Unlike the thicker floor build-up of a wood or steel joist system, the seven-layer panels are only 9-1/2 inches thick, similar to the thickness of concrete. This allowed the building to have a slightly smaller massing while still preserving high ceilings.
The decision to use a full post-and-beam wall structure, with glulam also manufactured by Structurlam, was driven by a previous CLT project, in which a hybrid system of load-bearing walls and post and beam created alignment challenges with the CLT panels; forgoing the load-bearing walls eliminated those issues.
The roughly 8-1/2-inch-square glulam columns are continuous for the height of the building—nearly 40 feet—a decision that cut down on the number of connections and allowed for more uniformity. In addition, the glulam offered predictable performance and uniformity versus solid-sawn lumber, as well as cost and supplier efficiencies for the project team.
For the roof system, the CLT panels extend beam to beam, eliminating any need for secondary structural supports that would interrupt open-concept offices.
On the exterior, CLT’s cantilever capabilities add key façade features. On the east-facing side, 5-foot balconies serve as a sunscreen as well as a tenant amenity. On the west-facing side, an angled roof overhang, ranging from 10 feet to 5 feet, enhances the entryway while protecting it from the elements.
APA-member Structurlam produces and certifies its CLT product in accordance with ANSI Standard PRG-320 for Cross-Laminated Timber, the standard that provides requirements and test methods for qualification and quality assurance of CLT. The standard includes seven stress classes covering major wood species in North America.
Like other wood products, CLT provides a familiar material for contractors and eliminates much of the hassle related to cast-in-place concrete; panels arrive ready to install with traditional tools. McLennan estimates the entire frame was erected in about three weeks, significantly less than the time required for concrete. In addition, the panels are one-sixth the weight of concrete.
A layer of architectural-grade Douglas fir on the exposed CLT serves as built-in finish for the ceilings, another key selling point; the glulam beams and columns, also exposed in most areas, coordinate perfectly.
“That helped us with leasability,” McLennan says. “They see it, and it’s beautiful from floor to ceiling.”
To read more case studies on commercial projects featuring engineered wood structural framing, become a member of APA Designers Circle at www.apawood.org/designerscircle. An online community for architects, engineers, and other members of the commercial building industry, Designers Circle provides timely information, technical resources, continuing education, and recommendations for innovative wood-frame construction.
About the Author
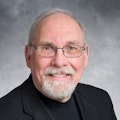