Mobilizing your job site to achieve a paperless project: fact or fiction?
Earlier this month, I attended the International Highway Engineering Exchange Program, or IHEEP, in Overland Park, Kansas. To kick off the event, I sat in on an IT round table for engineers and IT professionals to discuss the technical challenges facing the civil engineering community. Represented were members from various Department of Transportation agencies as well as the consultants who work with them.
One of the challenging questions posed was, “How can we better communicate with construction workers in the field?” They were trying to solve the challenge of getting high-quality drawings into the hands of field workers despite the bottleneck of limited computing power posed by the mobile devices used and preferred.
This challenge is nothing new to those in commercial construction. In fact, in the very short span of just two years, I’ve seen an evolution occur in the mobilization of jobsites. We’ve gone from paper-filled trailers to large screen monitors, creating paperless plan rooms. True mobility in the field has rapidly evolved from lock-box kiosks on each floor to laptops on rolling carts to tablets and iPads loaded with drawings sets stored in the cloud. PDF and cloud storage have been combined together to create a viable way for the designer and the field worker to view project content and collaborate in ways never before seen. WiFi-ready jobsites have gone from “nice to have” to “must have” status in just a little over a year.
Just last month I visited construction firm CW Driver on their 127,000-sf upscale redevelopment project site, where both contractor and sub were using mobile kiosks and iPads to electronically communicate on field issues, creating a virtually paperless— or at least “less paper”— jobsite. Leveraging the cloud, they store all submittals and RFIs electronically, linking them to current drawing sets for easy access by the subs.
When I asked Superintendent James Gentile how they managed to get all of the subs on board with the process, he stated, “We intentionally set up meetings prior to the start of a project to lay out our technical implementation plan of a paperless jobsite and then handpick subcontractors who see the value in what we’re trying to achieve.” When I asked him what benefits he sees from this interaction, he said, “Bottom line, our subs are able to do better work. When we as the GC can communicate to them clearly, and in a timely manner, what it is we need and expect from them, they are able to give us their best work.”
Call me cynical, but a statement like that had to be vetted. So I made my way over to the electrical contractor on the job, who just so happened to have an iPad in hand. I asked him how he felt the paperless jobsite worked in practicality. His response echoed what Gentile said: “We see the value in moving towards mobile devices to communicate on projects. In fact, my company specifically bought this iPad for me to use on this project because we’ve seen better results when partnering with a GC like CW Driver. They’ve committed to doing this job electronically, and they hold up their end of the bargain by making it easy for us to access the information we need. It has made communicating easier and friendlier than before.” That last statement got chuckles from others standing around us, but you could tell it was true. This jobsite was virtually paperless and downright friendly.
With technology making access to information easier than ever and collaboration on 2D and 3D PDFs increasing the clarity of communication, I wonder: what is your favored path to mobilize your jobsite? If you’ve made strides mobilizing your jobsite, care to share with us your implementation plan? There are lots of people interested in what you’ve found that works and, maybe more importantly, what hasn’t.
Editor's note: This is a sponsored article. All text and images were provided by the sponsor company.
About the Author
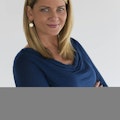
Sasha Reed
As Vice President of Strategic Development at Bluebeam, Inc., Sasha Reed collaborates with leaders in the architecture, engineering and construction industry to guide Bluebeam’s technology, partnerships and long-term goals. She joined Bluebeam in 2007 and co-created the Concierge Approach, a distinctly branded process of customer engagement, product feedback and solution delivery to which much of Bluebeam’s success is attributed, and which today is replicated at every organizational level.
Sasha is known industry-wide as a “conversation facilitator,” creating platforms for exchanges necessary to digitally advance the industry, including the BD+C Magazine Digital COM Blog, which she authors and manages. She’s been a featured presenter at numerous national and international conferences, including the 2014 Design-Build Institute of America (DBIA), Federal Project Delivery Symposium and NTI Danish BIM Conference. Sasha also co-chairs the Construction PDF Coalition, a grassroots effort to provide a common industry framework from which to create and maintain construction PDF documents, serves on the City College of San Francisco BIM Industry Council, and is Advisor to the Board of Direction for the National Institute of Building Sciences BuildingSMART Alliance.