A poll of contractors recounts perennial reasons for project delays
It is, perhaps, worth remembering that speed bumps to construction growth didn’t suddenly materialize with new leadership in Washington and 145% tariffs on imports.
A recently released poll of construction professionals found a sizable majority, 80%, that was optimistic about the demand for large-scale projects increasing over the next three to five years. However, the outlook of the survey’s 194 respondents was tempered by “challenges” that run the gamut from construction delays and budget overruns to schedule management, which is compounded by anticipated labor shortages.
The poll—conducted last summer by Endeavor Business Intelligence for Sherwin Williams Construction Solutions—also homed in on the benefits of shop-applied fireproofing for mitigating delays related to supply-chain snags, bad weather, and the lack of skilled field workers.
(Endeavor Business Intelligence is a division of Endeavor Business Media, which acquired BD+C last September.)
Respondents included managers or executives at general contractor firms with an average of one to five North American projects annually worth at least $30 million each. Nearly half of the qualified respondents are managers. Another 40% said they are executives, including at the C-suite level. Nearly seven in 10 respondents said they make the final purchasing decision.
A ‘host of obstacles’ to navigate
The survey largely corroborates what other reports tracking contractor attitudes have uncovered: that the industry’s growth is being stymied by “a host of obstacles that influence[s] virtually every type of project and industry vertical.”
More than half of the respondents—53%—identified budget overruns and 49% cited managing the schedule and meeting project timelines. Construction delays were a significant challenge with nearly nine in 10 respondents (87%) reporting delays in their projects. Material availability and supply chain issues stand out as the leading causes, impacting 71% of respondents, followed closely by weather related delays at 66%.
Delays can be caused by workplace accidents, too. The poll found 43% of respondents had projects where an accident, injury or death occurred at a significant height and 24% had projects where the building caught fire.
Sherwin Williams used the survey to advocate for shop-applied fireproofing. “Shops specializing in the application of fire protective coatings can complete the work faster because they have the equipment and experience, while also removing uncontrollable weather factors like rain, snow and cold that can delay a project,” the report states.
Over a third of respondents strongly agreed that they would consider shop-applied fireproofing if it could save them 10 weeks of overall project time. While passive fire protective coatings applied in a shop setting are often more expensive per gallon than their field application counterparts, they are superior when factoring in how they save time and money for overall megaproject construction. To that end, 72% of survey respondents reported a budget impact of up to 20% when using the field-applied fireproofing method.
The report also suggested that contractors could capitalize on opportunities from shop-applied fire coatings for protecting EV battery gigafactories, semiconductor fabrication plants, pharmaceutical manufacturing facilities, and other large-scale manufacturing buildings both during and after construction.
About the Author
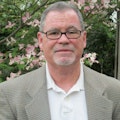
John Caulfield
John Caulfield is Senior Editor with Building Design + Construction Magazine.