Taking a page from Lean manufacturing for improved design review processes
As more building project teams look for ways to collaborate better, technology continues to provide solutions. Yet, as I learned from the experience of one of my customers, choosing the wrong technology can have an underwhelming effect, causing a team to simply swap out old challenges for new ones. The ideal technology solution would help the process run flawlessly, reducing rework, controlling costs and improving the overall project delivery.
Of course, before a technology solution can be determined, it is important to analyze the project management process to discover what actually needs to be streamlined. This is where designers and builders are starting to take cues from lean manufacturing, a method made popular by Toyota at the turn of the 20th century. Lean manufacturers aim to reduce waste from their overall process; they gain profit by creating value for the consumer through improved efficiencies.
The Lean Construction Institute is helping designers and builders understand the benefits of “lean thinking.” On their website, they illustrate how this type of project management system helps redefine control “from ‘monitoring results’ to ‘making things happen’.” Specifically, the group explains that lean thinking is:
Decentralizing decision-making through transparency and empowerment. This means providing project participants with information on the state of the production systems and empowering them to take action. In summary, Lean Construction is a production management-based project delivery system emphasizing the reliable and speedy delivery of value. It challenges the generally accepted belief that there are always trade-offs between time, cost and quality.
The key word here is “value”. In lean manufacturing, they often measure the “value add” versus “non-value add” parts of a process. The goal is to minimize the non-value add parts as much as possible.
To this end, I recently presented a customer case study at the Sustainable Manufacturer Summit in Naperville, IL. The case study focused on lean as it applies to the design review process. Unlike typical manufacturers who mass produce the same product, this particular manufacturer had a team of engineers devoted to modifying existing products. They revised the designs to fit unique, one-off production requests by reviewing both designs with CAD consultants and dealers working directly with the customer. Their approach offers some useful insight that is applicable to other technical design review processes. I will step through them for you below.
First, define the current process.
This customer analyzed their established process, capturing both total number of steps taken to complete a review cycle and the total time spent on it. This provided a baseline for comparing other technologies against it so they could more accurately track the benefits of each pilot test.
During this step, they defined three categories of custom design drawings: Simple, Moderate and Complex, with fluctuation on volume based on customer demand.
Then, measure the current process.
For this customer, reviewing drawings on paper required a total of 10 steps. These steps included printing, marking up, saving and sharing. Simple drawings took on average nine minutes to review, with only 35% of that time devoted to the value add action of actually reviewing and marking up the drawings. Moderate drawings took over 13 minutes, with about 58% devoted to marking up, and Complex drawings took 17 minutes with 83% devoted to markup.
Technology Implementation #1
Reviewing drawings with a screen capture solution reduced the steps from 10 to nine (see diagram 1). However, this created a new issue for the reviewers. Since the screen capture software saved raster images of the drawings rather than a vector PDF of the drawing, it taxed their hardware resources. They could not have more than one drawing open at a time without crashing their computers. Although it eliminated one step from the overall process, it actually added more time. In fact, for Moderate drawings, it took them nearly twice as long to review electronically than marking up by hand.
Diagram 1:
Total steps saved – Image courtesy of Bluebeam customer
Consequently, the firm decided to redefine their technology needs. The three new key components they wanted were high-quality, vector-based PDFs with 2D and 3D capability, robust markup features, and the ability to track changes.
Technology Implementation #2
For their second implementation, they found our software—and the results were significant. Reviewing drawings with Revu cut the steps from 10 to six. It also cut the review time for Simple drawings from nine minutes down to four. And of those four minutes, 98% was spent reviewing or doing value add work. Similar results were found with Moderate and Complex drawings, with a time savings of 32% and 38%, respectively (see diagram 2).
Diagram 2:Overall breakdown of results by time; the blue line represents time to do “value add” design work – Image courtesy of Bluebeam Customer
The pilot program took place over a four month period. The time savings tracked during those four months had the potential to add up to a 12 hours per week, or $45K annually, if extrapolated over a 12 month period.
As more General Contractors apply lean manufacturing principles to construction, they will change the way project teams look at design collaboration, scheduling and risk. They will implement Integrated Project Delivery (IPD) methods, bringing together traditionally siloed project partners and creating greater transparency through shared risk. Coordination meetings will bring key partners together earlier in the process. Teams will focus on improving efficiencies in everything from scheduling to prefabrication of components, rethinking and “leaning” out the process. If a technology solution creates waste, lean thinking encourages them to go back to the drawing board to find another solution. They will never get stuck in one mode of working: processes will always evolve, just as technology solutions do.
Is your firm applying lean principles? What has the experience been like?
Editor's note: This is sponsored content. Images and text were provided by the sponsor company.
About the Author
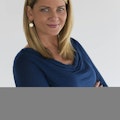
Sasha Reed
As Vice President of Strategic Development at Bluebeam, Inc., Sasha Reed collaborates with leaders in the architecture, engineering and construction industry to guide Bluebeam’s technology, partnerships and long-term goals. She joined Bluebeam in 2007 and co-created the Concierge Approach, a distinctly branded process of customer engagement, product feedback and solution delivery to which much of Bluebeam’s success is attributed, and which today is replicated at every organizational level.
Sasha is known industry-wide as a “conversation facilitator,” creating platforms for exchanges necessary to digitally advance the industry, including the BD+C Magazine Digital COM Blog, which she authors and manages. She’s been a featured presenter at numerous national and international conferences, including the 2014 Design-Build Institute of America (DBIA), Federal Project Delivery Symposium and NTI Danish BIM Conference. Sasha also co-chairs the Construction PDF Coalition, a grassroots effort to provide a common industry framework from which to create and maintain construction PDF documents, serves on the City College of San Francisco BIM Industry Council, and is Advisor to the Board of Direction for the National Institute of Building Sciences BuildingSMART Alliance.