Rotherhithe is a peninsula district located 4.5 kilometers east of central London. The district is directly adjacent to the 53-acre Canada Water, a four-billion-British pound (US$4.8 billion) mixed-use redevelopment that, when completed, will create a new town center with 3,000 homes, two million sf of office space, one million sf of retail/leisure/entertainment/community spaces, and 12 acres of new public space. The 35 to 40 buildings at Canada Water will be net-zero energy by 2030. Phase one of this project is scheduled for completion in the third quarter of 2024.
Canada Water and Rotherhithe are within the borough of Southwark, whose Council commissioned the architecture firm IF_DO to design The Hithe, a 200-sm (2,153-sf) building on what had been a vacant 283-sm lot in Rotherhithe, that provides 12 units of business incubator workspace for startups.
The key to this building is that it can be disassembled and relocated relatively easily and as needed. The Hithe was completed at a construction cost of 400,000 pounds in late 2021, and started accepting tenants in early 2022.
IF_DO designed The Hithe (whose name harkens back to the Old English term for a landing place or small port) in collaboration with the social enterprise Meanwhile Space, which is also leasing the largest unit in the building; the general contractor and fabricator Weber Industries; and the structural engineer Elliott Wood Partnership. The Council identified the “meanwhile” use of The Hithe as up to 11 years, at which point it is likely to be taken down and reassembled in another location as the district’s redevelopment evolves.
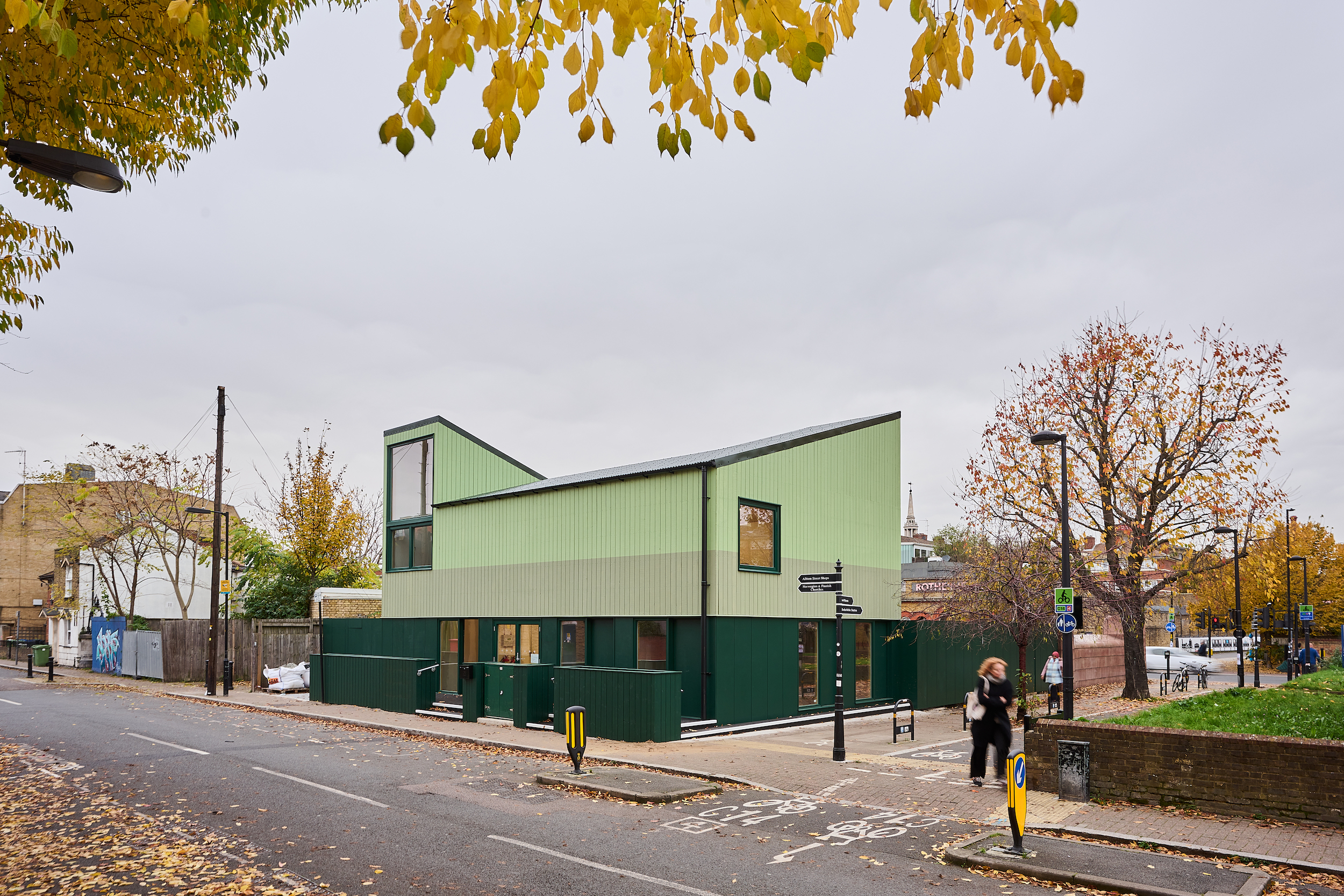
IF_DO refers to The Hithe as “social infrastructure,” and contends that it acts as a “hinge” between the existing community and the new developments around it.
Eddie Bridgeman, Meanwhile Space’s Executive Director, explains that shipping containers—previously a “go-to” option for temporary buildings—would have been the wrong aesthetic choice for the Rotherhithe project. “To re-use the building again and again, maintain a quality structure and look that could be tweaked for different locations, we needed an alternative.”
Thomas Bryans, RIBA, IF_DO’s Director, adds that the community wanted a building that didn’t look temporary. “We have had conversations with Meanwhile Space for a while about the potential of relocatable micro work units, and The Hithe was the perfect opportunity to start testing some of those ideas.”
Indeed, prior to its involvement in The Hithe, If_DO had designed for Meanwhile Space a 350-sm short-term refurbishment on Lower Marsh, Waterloo, called Granby Space, which closed after five years. The Hithe, states IF_DO, “represents a departure for Meanwhile Space,” its first full-blown venture into circularity, the concept of reusing redundant space and materials more productively and to lower a building’s carbon footprint and waste.
Bryans tells BD+C that his firm is “constantly investigating” circularity. He points specifically to a recent project IF_DO designed for U.K. property developer Related Argent that wrapped an electrical substation at Brent Cross Town in North West London with a massive kaleidoscopic piece of public art made mostly of piping from the oil industry.
For The Hithe, IF_DO consulted Circular Construction in Regenerative Cities (CIRCuIT), particularly during the project’s technical design stage. One of CIRCuIT’s “key inputs,” says Bryans, was factoring the life cycle and carbon analysis costs into the impact of designing for disassembly and reuse, compared to more traditional forms of construction.
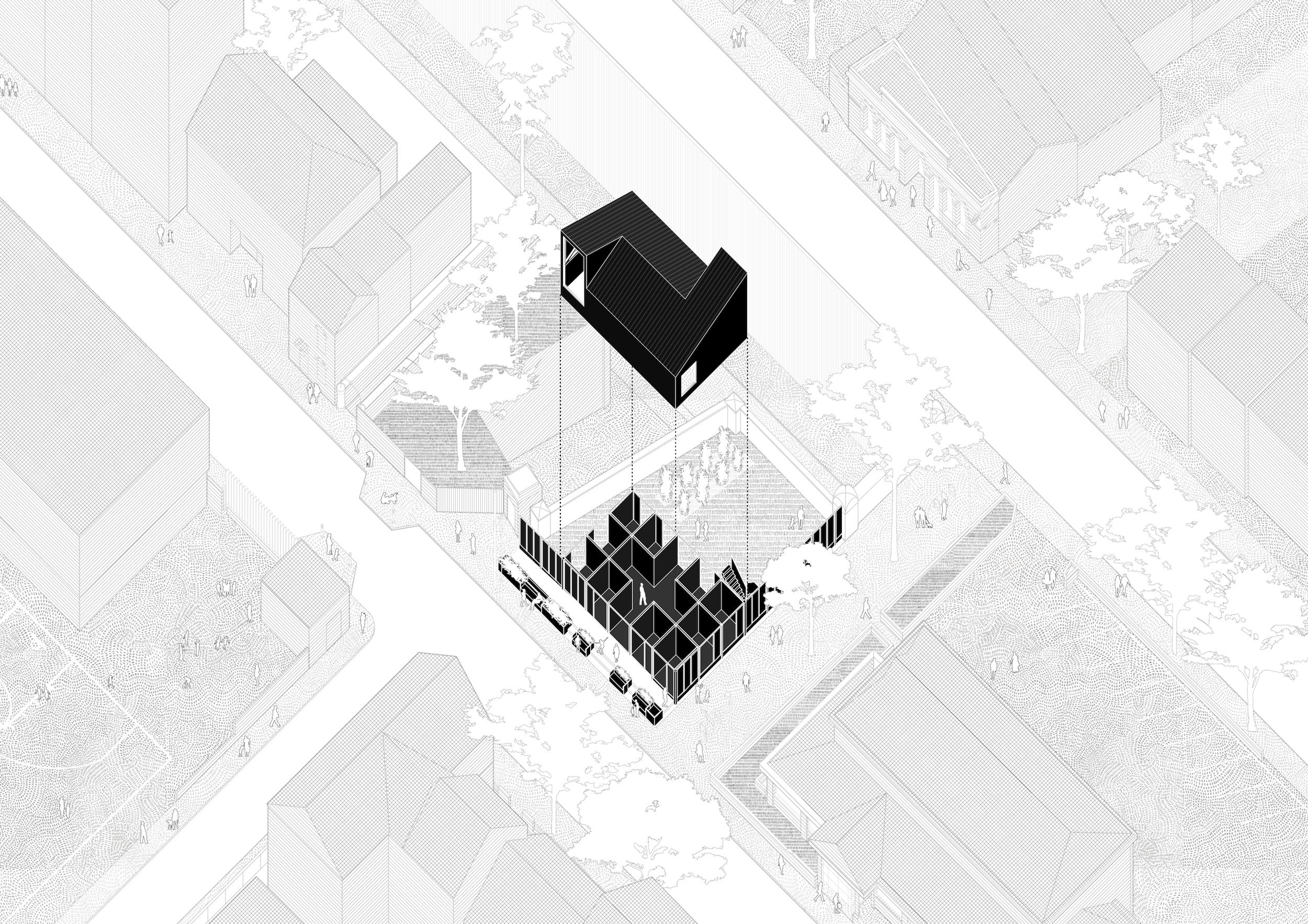
The Hithe was constructed using lightweight steel and timber framing. Bryans says almost all of the building’s components were prefabricated in Weber Industries’ workshop near the jobsite. The ground floor of the building was designed as volumetric modules to make their future relocation easier, and the first floor with panelized glulam framing and structural insulated panels (SIPs) that were built onto existing foundations, remnants of three houses that had been demolished many years earlier.
Inside The Hithe, the timber structure and services are exposed. Its studios are arranged around a ground-floor gathering space that is linked to a kitchen and a yard to the north of the site that has been transformed into a planted outdoor social space. Two larger workspaces are located on the first floor. And all the units are accessed externally, thereby reducing the need for circulation corridors.
“Our vision for a fully demountable building that acts as a beacon for Albion Street has come to life,” says Helen Dennis, Southwark Council’s cabinet member for climate emergency and sustainable development. “This sustainable hub can be redeployed to sites across the borough, meaning in term other areas can reap similar economic and social rewards.”
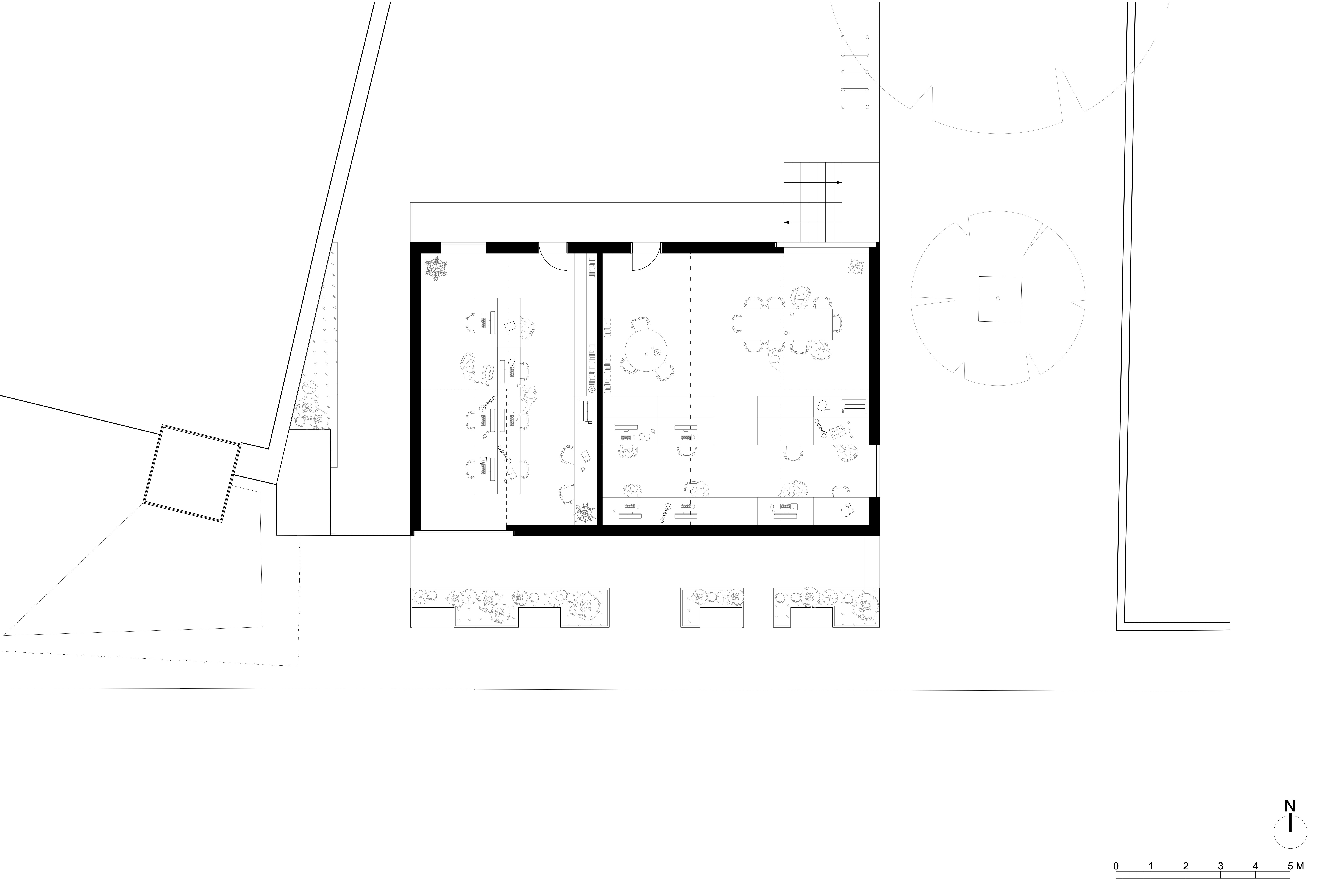
Related Stories
Modular Building | Mar 20, 2023
3 ways prefabrication doubles as a sustainability strategy
Corie Baker, AIA, shares three modular Gresham Smith projects that found sustainability benefits from the use of prefabrication.
Building Tech | Mar 14, 2023
Reaping the benefits of offsite construction, with ICC's Ryan Colker
Ryan Colker, VP of Innovation at the International Code Council, discusses how municipal regulations and inspections are keeping up with the expansion of off-site manufacturing for commercial construction. Colker speaks with BD+C's John Caulfield.
Affordable Housing | Mar 14, 2023
3 affordable housing projects that overcame building obstacles
These three developments faced certain obstacles during their building processes—from surrounding noise suppression to construction methodology.
AEC Innovators | Mar 3, 2023
Meet BD+C's 2023 AEC Innovators
More than ever, AEC firms and their suppliers are wedding innovation with corporate responsibility. How they are addressing climate change usually gets the headlines. But as the following articles in our AEC Innovators package chronicle, companies are attempting to make an impact as well on the integrity of their supply chains, the reduction of construction waste, and answering calls for more affordable housing and homeless shelters. As often as not, these companies are partnering with municipalities and nonprofit interest groups to help guide their production.
Modular Building | Mar 3, 2023
Pallet Shelter is fighting homelessness, one person and modular pod at a time
Everett, Wash.-based Pallet Inc. helped the City of Burlington, Vt., turn a municipal parking lot into an emergency shelter community, complete with 30 modular “sleeping cabins” for the homeless.
Multifamily Housing | Mar 1, 2023
Multifamily construction startup Cassette takes a different approach to modular building
Prefabricated modular design and construction have made notable inroads into such sectors as industrial, residential, hospitality and, more recently, office and healthcare. But Dafna Kaplan thinks that what’s held back the modular building industry from even greater market penetration has been suppliers’ insistence that they do everything: design, manufacture, logistics, land prep, assembly, even onsite construction. Kaplan is CEO and Founder of Cassette, a Los Angeles-based modular building startup.
Affordable Housing | Feb 15, 2023
2023 affordable housing roundup: 20+ multifamily projects
In our latest call for entries, Building Design+Construction collected over 20 multifamily projects with a focus on affordable housing. Here is a comprehensive list of all projects in alphabetical order.
Data Centers | Feb 6, 2023
Modular electric rooms are the new normal
Southland Industries breaks down the prefabrication benefits of Modular Electric Rooms (MERs).
Multifamily Housing | Feb 3, 2023
HUD unveils report to help multifamily housing developers overcome barriers to offsite construction
The U.S. Department of Housing and Urban Development, in partnership with the National Institute of Building Sciences and MOD X, has released the Offsite Construction for Housing: Research Roadmap, a strategic report that presents the key knowledge gaps and research needs to overcome the barriers and challenges to offsite construction.
Augmented Reality | Jan 27, 2023
Enhancing our M.O.O.D. through augmented reality therapy rooms
Perkins Eastman’s M.O.O.D. Space aims to make mental healthcare more accessible—and mental health more achievable.