Mass timber is poised to join concrete, steel, and light-wood framing as a primary structural material for multifamily projects.
Mass timber construction involves the use of prefabricated wood components on a building’s load-bearing walls, roofs, floors, beams, and columns.
Its advocates say building with mass timber creates less waste, leaves a lighter carbon footprint (because wood sequesters carbon), and can be quicker and quieter than other construction modes. Some go so far as to claim that exposed wood has tangible health and wellness benefits for building occupants.
Europe has been at the forefront of the movement; hundreds of mass timber office buildings dot the continent. In North America, mass timber adoption has been constrained by code restrictions that made it financially impractical, especially for multifamily projects.
That situation may be changing. “Architects and developers are becoming increasingly interested in the technology,” said Mitch Warren, who represents Kalesnikoff, a Canadian mass timber supplier.
That interest is being fueled by the 2021 edition of the International Building Code, which increased the maximum allowable height for mass timber structures in the U.S. to 18 stories. In Canada, the 2020 National Building Code allows wood buildings up to 12 stories high.
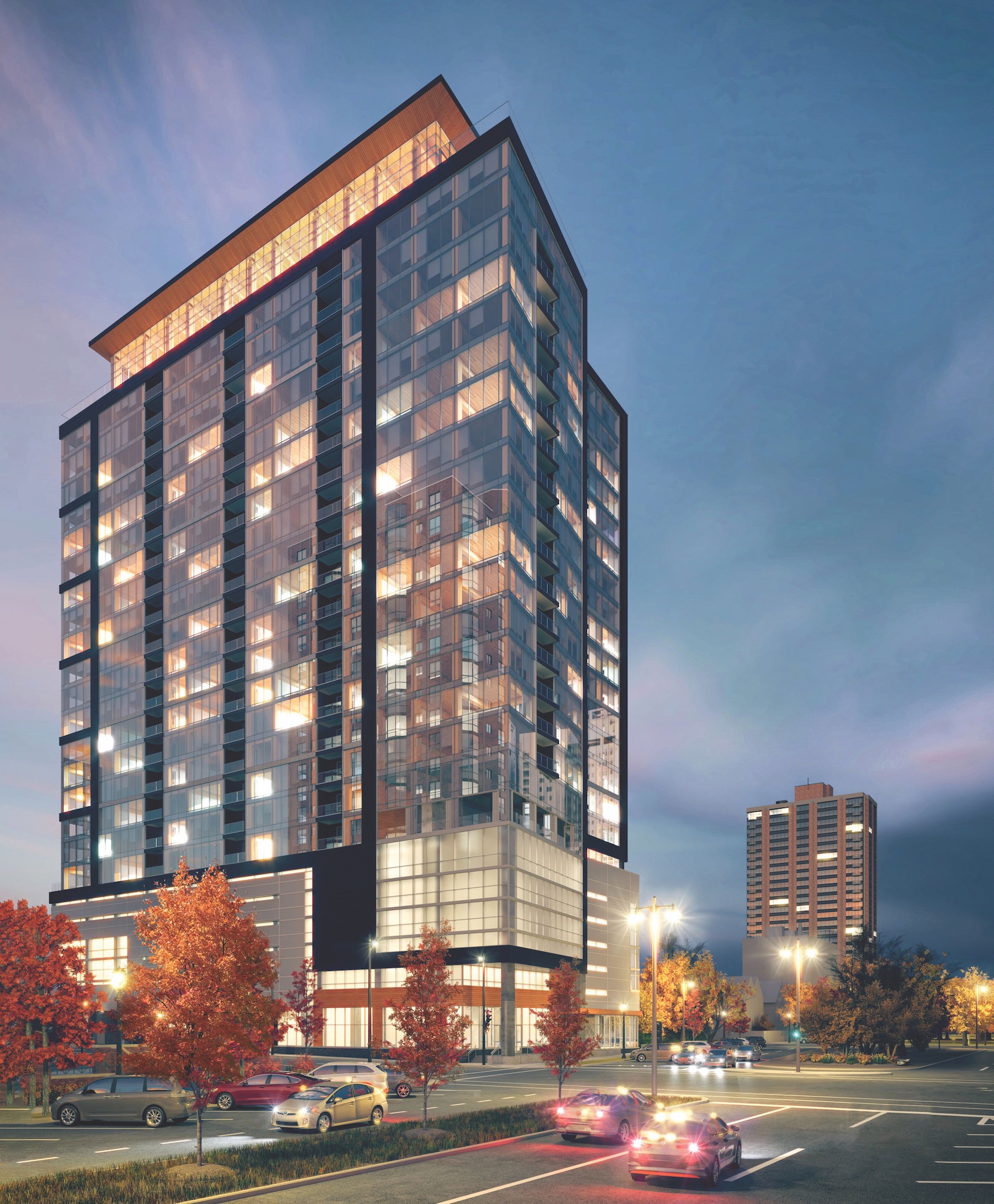
California, Maine, Oregon, Utah, Virginia, and Washington have adopted the IBS update in some form, as have Denver and Austin, Texas. Georgia, Idaho, and Wisconsin are in the process of adopting the new IBC height allowances.
Other jurisdictions are expected to follow their lead, paving the way for a new generation of tall mass timber residential buildings to rise across the urban America landscape.
Several trailblazing residential mass timber projects have been completed or are under construction in the U.S.:
- Carbon 12, an eight-story structure housing 14 condominiums; it opened four years ago in Portland, Ore.
- The Canyons Apartments, six stories and 65 feet in height, with 70 ADA-compliant apartments, also in Portland; it opened in 2020.
- Railyard Flats, a four-story (3-over-1), 41-unit rental property in Sioux Falls, S.D.; it opened last September.
- INTRO, a 297-unit tower in Cleveland, started leasing earlier this year; at nine floors over a two-story podium, it will briefly hold the record as the tallest mass timber residence in the U.S.
- T3 Eastside, a heavy timber office/residential complex with 15 boutique lofts, under construction in Austin, Texas.
- Ascent, a 25-story apartment tower in Milwaukee which, upon completion this August, will be the world’s tallest mass timber structure (284 feet), surpassing Mjøstårnet in Brumunddal, Norway (277 feet).
ADVICE FROM LEADING MASS TIMBER CONSTRUCTION PRACTITIONERS
We asked architects, builders, and developers involved in “big timber” work to share their advice and insights. Here’s what they told us.
Make sure big timber pencils out. There’s a tipping point, around six stories, below which other construction methods, notably light-frame and post-tensioned concrete, are usually more economical than mass timber. “Building a five-story apartment building out of mass timber carries a sizable cost premium that most developers probably couldn’t justify,” said Laura Hollier, AIA, LEED GA, an architect at Nashville design firm Hastings.
Jason Korb, AIA, Principal at Korb + Associates Architects, the design firm for Ascent, said, “I don’t believe anything less than 10 stories has a fighting chance to beat post-tensioned concrete.”
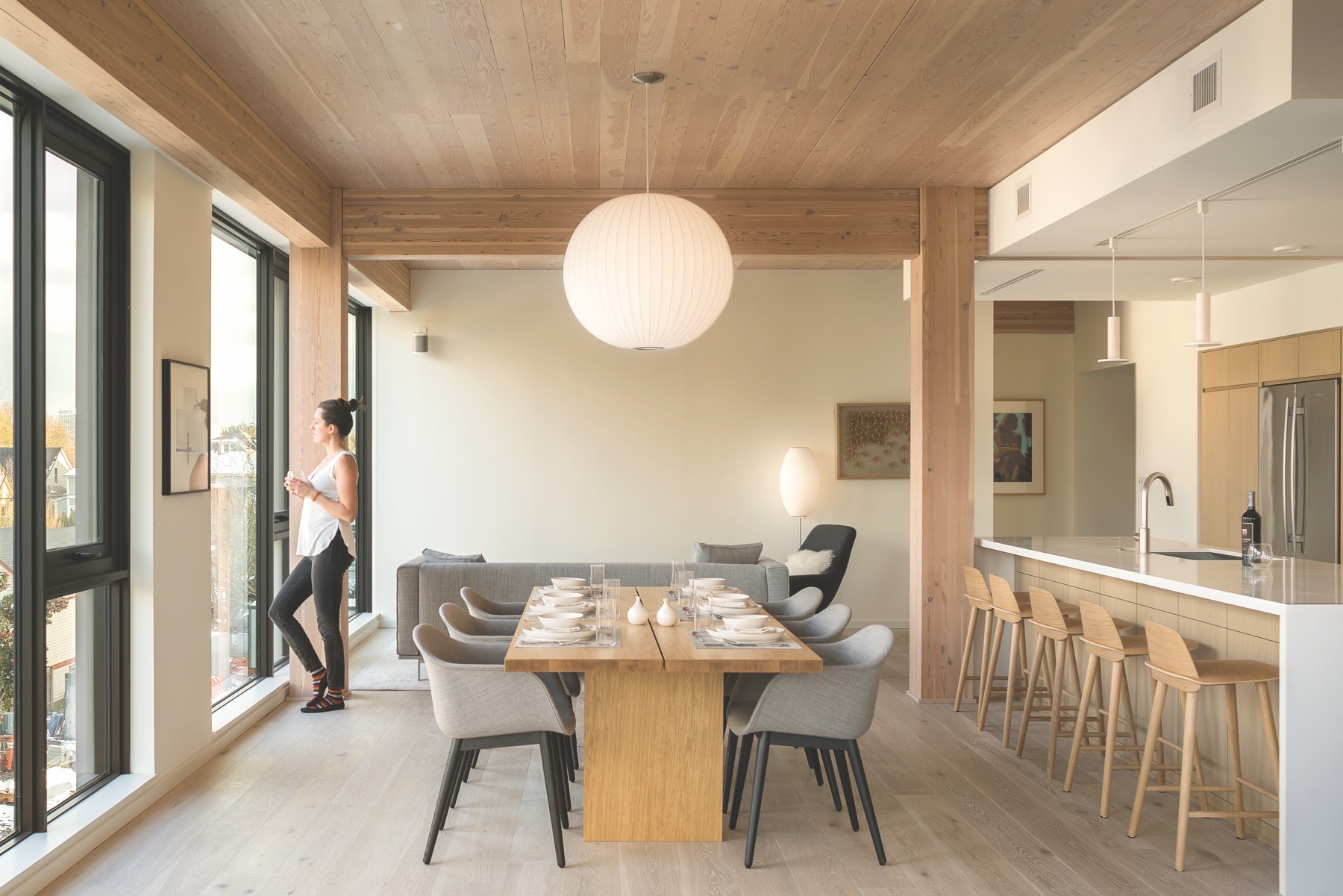
But Ben Kaiser, Founder of Kaiser + Path, the designer/developer of The Canyons Apartments, said that project’s 5-over-1 structure proved economical. “The additional cost is offset because mass timber construction requires fewer workers and can be up to 25% faster,” he said.
Engage code officials early. “Have the building department and the fire marshal in the room at the start, along with the planning department,” said John Mitchell, LEED AP BD+C, Associate Partner, Hartshorne Plunkard Architecture (HPA), the design firm for INTRO.
Wiss, Janney, Elstner, the fire consultant on INTRO, used extensive approved fire-testing documentation to make the case for the building’s safety, but “it took 18 months of meetings to get approvals” from code authorities in Cleveland, said Mitchell.
State officials in Wisconsin required 14 fire resiliency tests of Ascent’s structural decks, beams, and columns before they would grant a variance from the state’s building code, which does not permit mass timber high-rises. As a result of the positive experience with Ascent, Wisconsin authorities are preparing draft guidelines that would allow mass timber structures under the statewide building code.
Get your supplier and installer on board from the start. “Each manufacturer’s product varies in wood species as well as panel sizes and thicknesses, so unless you select the manufacturer on the front end, it is hard to efficiently design the superstructure,” said Hollier.
The vast forests of Douglas fir in British Columbia and the Pacific Northwest are home to numerous suppliers. Southern yellow pine is becoming a source of cross-laminated timber. SmartLam has such a CLT plant in Dothan, Ala., and Structurlam, the big Canadian supplier, is building its first U.S. CLT factory in Conway, Ark.
Europe also has experienced suppliers. INTRO’s timber came from from an Austrian supplier, Binderholz. Ascent’s glulam came from Wiehag; its CLT, from KLH, both Austrian. StuctureCraft sourced the DLT glulam beams and columns for Railyard Flats from another Austrian firm, Hasslacher, just before the Covid pandemic jacked up lumber prices. “We got lucky on the timing,” said Anne Haber, who, with her father, Jeff Scherschligt, President of Pendar Properties, developed the 41-unit rental project in Sioux Falls, S.D.
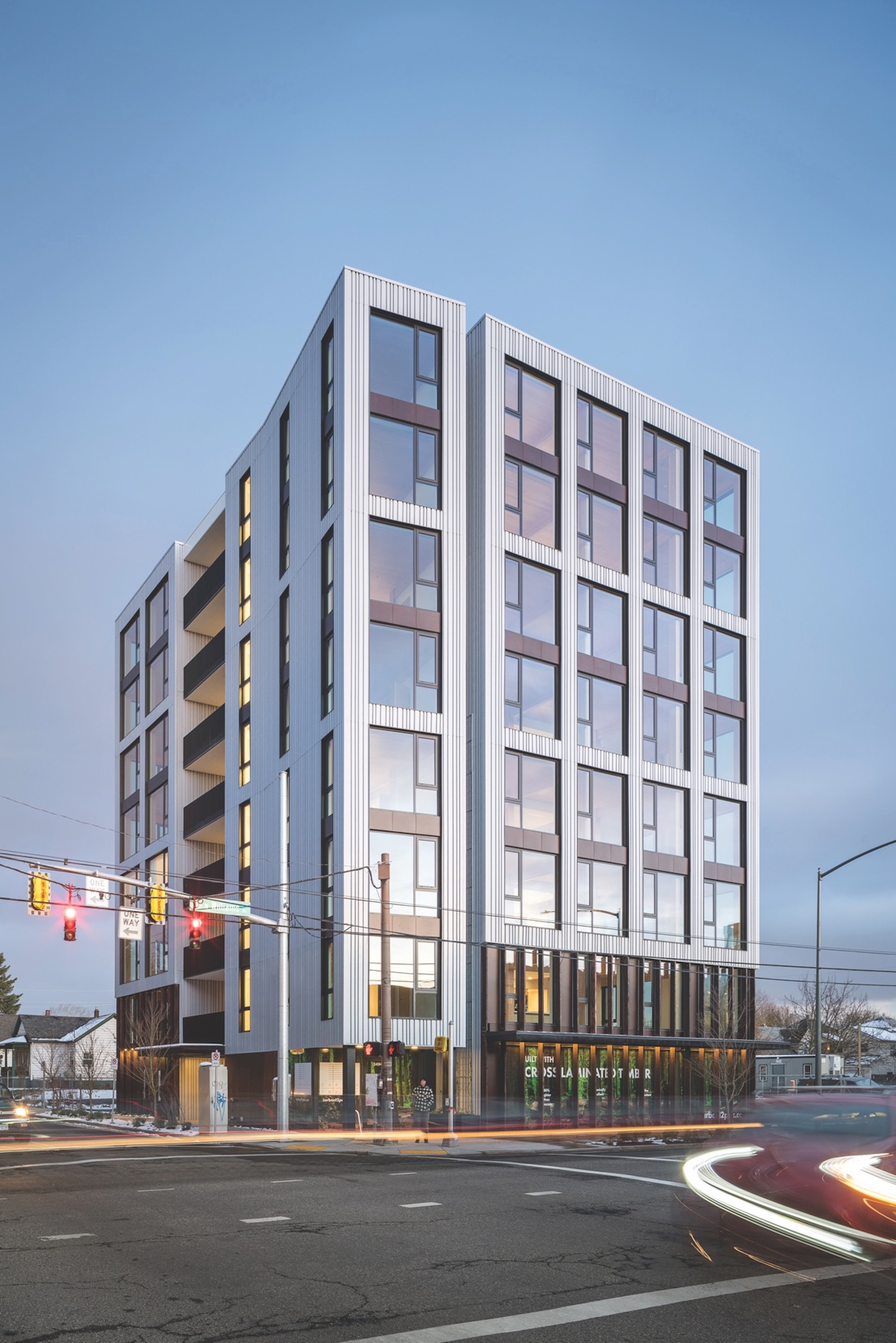
Select wood from sustainable sources. The two most well-known certification systems are the Forest Stewardship Council (FSC) and the Sustainable Forestry Institute (SFI).
Take advantage of wood’s physical attributes. Because mass timber weighs about one-fifth that of concrete, it can produce valuable efficiencies. “On Ascent, we drove half as many piles as we would have with concrete,” said Korb. Mass timber also has a high strength-to-weight ratio, which benefits seismic performance.
Advocates say building with mass timber is faster than building with concrete. “We were able to do 70,000 square feet of deck every five days on Ascent,” said Kolb. Kaiser Group’s Ben Kaiser also said it took just four carpenters five days for each floor of Carbon 12. “That would have taken two-and-a-half weeks with concrete,” he said.
Foster team cohesion. The developer and the AEC team need to be pulling in the same direction. “A successful multifamily mass timber building takes ongoing collaboration to make it work,” said Ted Panton, AIA, Principal and Design Director at GGLO.
Plumbers, electricians, and key trades should be engaged early. “They will be interfacing with the structure much more than they do on a typical project, so it’s important to educate them, discuss options, and coordinate with them throughout the process,” said Jeff Morrow, Preconstruction Manager at Timberlab, the mass timber construction division of Swinerton.
Be prepared to referee MEP meetings. The biggest selling point for residential mass timber projects is the exposed wood in the living units and common areas. That beauty factor can complicate the routing of exposed HVAC ductwork and MEP systems. “We had to coordinate all the trades into a few small soffits and drop ceilings,” said Taylor Cabot, project manager on Carbon 12. “In a typical 1,500-square-foot unit they were all vying for space in a 200-square-foot soffit.”
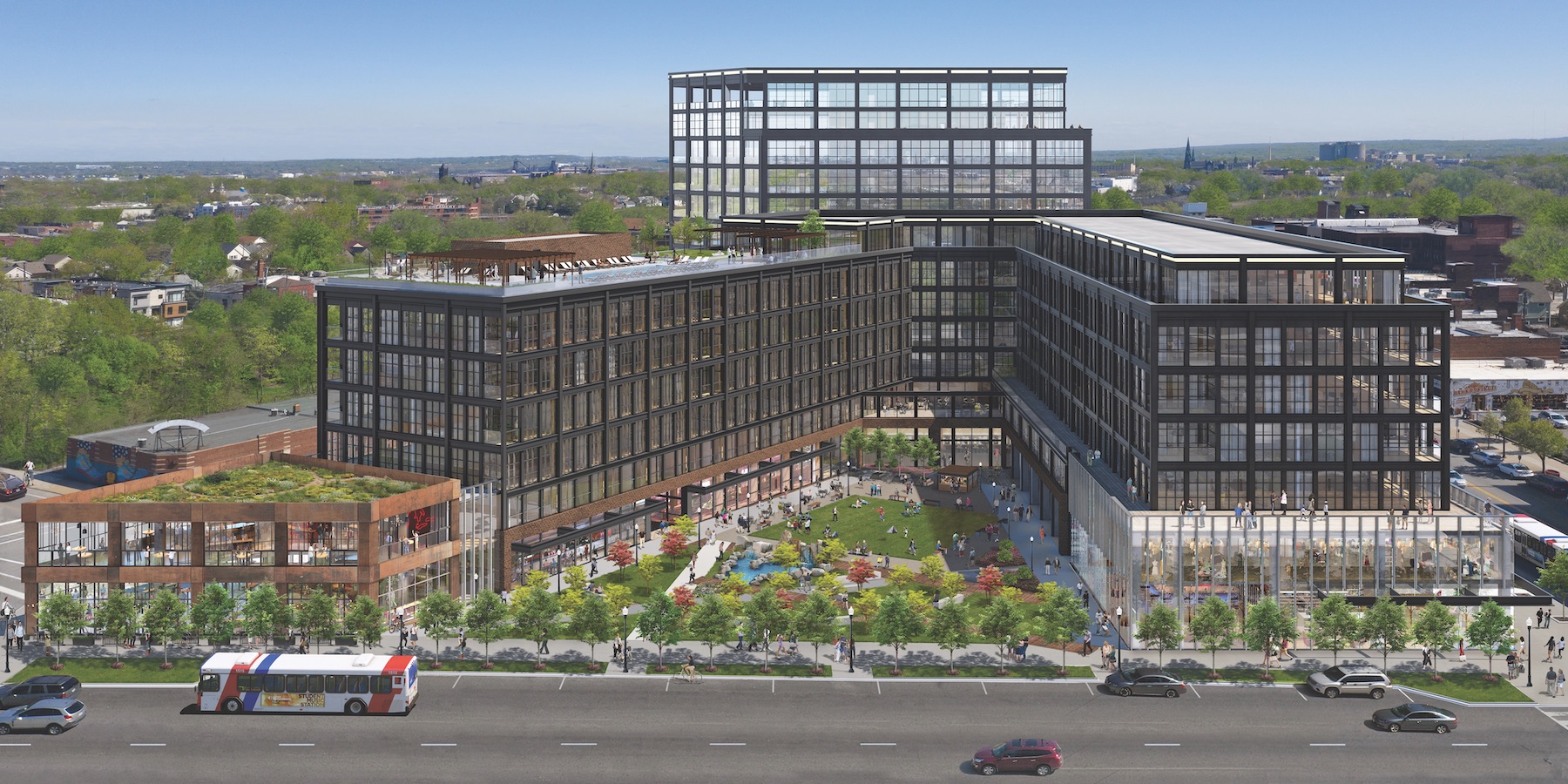
MEP teams, BIM modelers, and timber suppliers have to coordinate early on the BIM model to minimize the number and size of MEP penetrations. “Because our panels were coming in from Austria, we had to predrill a lot of holes,” many of which proved to be redundant, said HPA’s Mitchell. “We wound up filling as many holes as we drilled.”
Address the acoustics. Controlling sound transmission between multifamily units in mass timber buildings can be a problem. A concrete or gypsum-based topping layer can be applied above the floor/ceiling assembly to improve acoustical performance while preserving the exposed wood ceiling for residents. Decouplers, such as floor underlayments and acoustic mats, can also reduce structure-borne vibrations and block sound transfer, said Kalesnikoff’s Warren.
For INTRO’s floors, 3/8-inch acoustic mats were placed on top of the CLT flooring panels, and 2-3 inches of concrete was poured on the mats. “You can’t hear a thing,” said Mitchell.
Protect the wood. Mass timber panels need to be protected from exposure to the elements during shipment and on the job site. “Make sure all the wood is dried out before it’s covered up,” said Hollier.
Recalibrate your construction waste. Building modules arrive at the job ready to be assembled, which can drastically cut construction waste on the site. “A superintendent on a mass timber job recently told me he had to send most of his trash bins away empty because so little waste had been generated,” said Tom Chung, FAIA, LEED AP BD+C, Principal at Leers Weinzapfel Associates, which designed the mass timber Adohi Hall student resident at the University of Arkansas.
Market wood’s human appeal. Railyard Flats, which occupies an old train switching yard overlooking the Big Sioux River, was fully leased in two months, largely to younger renters and seniors nearing retirement. “The timber was a huge marketing piece for us,” said Pendar Properties’ Haber. “Everybody liked the warmth of the wood.”
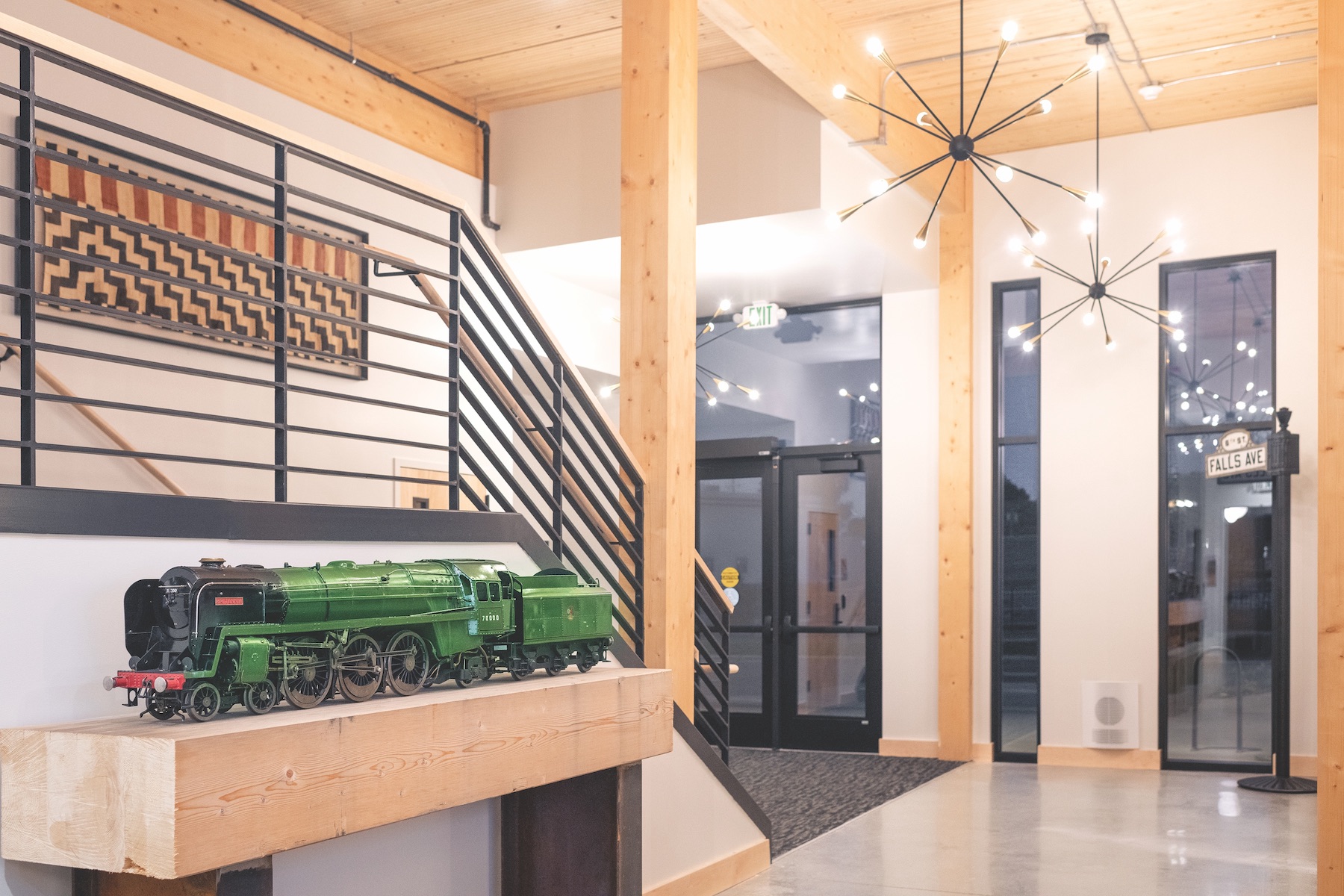
Dispel any rumors of timber’s flammability. Recent fire resistance tests demonstrate that CLT and related products have inherent fire-resistant properties and outperform code requirements. “Rather than flashing up like kindling in a campfire, it’s more like the big log that’s really hard to light,” said Hardy Wentzel, CEO of Structurlam Mass Timber Corporation. “When mass timber walls are protected with gypsum wallboard, as the code requires, they can achieve nearly damage-free performance from a fire.”
Check out possible financial incentives. There’s a growing list of grants and awards via the Timber Innovation Act, the USDA Wood Innovations grant program, and Softwood Lumber Board grants.
MASS TIMBER INNOVATORS KEEP PUSHING THE LIMITS
Mass timber pioneers are forging ahead with new projects. Pendar Properties’ father-daughter team of Scherschligt and Haber is developing a $225 million complex in Sioux Falls that will combine a concrete office tower and parking garage with a pair of six-story mass timber edifices totaling 236 rental units.
Korb + Associates has two mass timber enterprises in the works: 2700 Sloat, a 12-story, 400-unit condominium development in San Francisco that will reach 125 feet in height; and Adelaide Point, a 30-acre, $250 million development on Lake Michigan in Muskegon, Mich., that will include a six-story, 300-unit luxury condominium residence.
Mass timber is not going to replace concrete and steel, but “it has a place in the market” for residential buildings with a two-hour fire rating in the nine- to 15-story range, said HPA’s Mitchell.
Tim Gokhman, Managing Director, New Land Enterprises, is more optimistic about the technology. “Mass timber is doing for buildings what Tesla did for electric vehicles,” he said. “It’s beautiful, lighter, faster, more precise, and sustainable.”
Related Stories
AEC Innovators | Mar 2, 2023
Turner Construction extends its ESG commitment to thwarting forced labor in its supply chain
Turner Construction joins a growing AEC industry movement, inspired by the Design for Freedom initiative, to eliminate forced labor and child labor from the production and distribution of building products.
Multifamily Housing | Mar 1, 2023
Multifamily construction startup Cassette takes a different approach to modular building
Prefabricated modular design and construction have made notable inroads into such sectors as industrial, residential, hospitality and, more recently, office and healthcare. But Dafna Kaplan thinks that what’s held back the modular building industry from even greater market penetration has been suppliers’ insistence that they do everything: design, manufacture, logistics, land prep, assembly, even onsite construction. Kaplan is CEO and Founder of Cassette, a Los Angeles-based modular building startup.
AEC Innovators | Feb 28, 2023
Meet the 'urban miner' who is rethinking how we deconstruct and reuse buildings
New Horizon Urban Mining, a demolition firm in the Netherlands, has hitched its business model to construction materials recycling. It's plan: deconstruct buildings and infrastructure and sell the building products for reuse in new construction. New Horizon and its Founder Michel Baars have been named 2023 AEC Innovators by Building Design+Construction editors.
AEC Tech | Jan 27, 2023
Key takeaways from Autodesk University 2022
Autodesk laid out its long-term vision to drive digital collaboration through cloud-based solutions and emphasized the importance of connecting people, processes and data.
AEC Tech Innovation | Jan 24, 2023
ConTech investment weathered last year’s shaky economy
Investment in construction technology (ConTech) hit $5.38 billion last year (less than a 1% falloff compared to 2021) from 228 deals, according to CEMEX Ventures’ estimates. The firm announced its top 50 construction technology startups of 2023.
AEC Tech Innovation | Jan 14, 2023
CES recognizes a Dutch firm’s wearable technology for construction management
The firm’s TokenMe product offers construction managers a real-time crowd- and asset-tracking solution via low-power, location-aware radio and RFID tags and multiple sensors through which data are processed with cloud-based artificial intelligence.
Digital Twin | Nov 21, 2022
An inside look at the airport industry's plan to develop a digital twin guidebook
Zoë Fisher, AIA explores how design strategies are changing the way we deliver and design projects in the post-pandemic world.
Giants 400 | Nov 14, 2022
4 emerging trends from BD+C's 2022 Giants 400 Report
Regenerative design, cognitive health, and jobsite robotics highlight the top trends from the 519 design and construction firms that participated in BD+C's 2022 Giants 400 Report.
Contractors | Nov 14, 2022
U.S. construction firms lean on technology to manage growth and weather the pandemic
In 2021, Gilbane Building Company and Nextera Robotics partnered in a joint venture to develop an artificial intelligence platform utilizing a fleet of autonomous mobile robots. The platform, dubbed Didge, is designed to automate construction management, maximize reliability and safety, and minimize operational costs. This was just one of myriad examples over the past 18 months of contractor giants turning to construction technology (ConTech) to gather jobsite data, manage workers and equipment, and smooth the construction process.
Architects | Nov 10, 2022
What’s new at 173 architecture firms for 2022
More than 295 U.S. architecture and architecture-engineering (AE) firms participated in BD+C's 2022 Giants 400 survey. As part of the Giants survey process, participating firms are asked to describe their most impactful firm innovations and noteworthy company moves in the past 12 months. Here is a collection of the most compelling business and project innovations and business moves from the 2022 Architecture Giants.